From 01269a008e5231cc0e6ca7872fa7a4435fd33412 Mon Sep 17 00:00:00 2001 From: Mohammed Omer <momer93@hotmail.com> Date: Wed, 5 May 2021 06:40:27 +0200 Subject: [PATCH] edits --- docs/machines/3DPrinter.md | 157 +++++++++++++++++--------- docs/machines/DesktopLaserCutter.md | 8 +- docs/machines/LargeFormatCNCRouter.md | 59 +++++++++- docs/machines/LargeScale3DPrinter.md | 9 +- docs/machines/Plasma Cutter.md | 28 ++++- 5 files changed, 202 insertions(+), 59 deletions(-) diff --git a/docs/machines/3DPrinter.md b/docs/machines/3DPrinter.md index ae49a05..3c6f5ef 100644 --- a/docs/machines/3DPrinter.md +++ b/docs/machines/3DPrinter.md @@ -1,12 +1,12 @@ # Table of Contents -[[_TOC_]] +[_TOC_] # Desktop 3D Printer Preliminary research was carried out to see which open source designs and commercial 3D are popular in the 3D printer community. These will be used as a starting point for the development of the desktop 3D Printer. Various repositories such as Youtube, Github, Instructables, GrabCad, Thingiverse, Personal Blogs and Technical Forums were searched. -## Popular Open Source/Kit 3D Printers +# Popular Open Source/Kit 3D Printers 1. The [Prusa i3MK3](https://www.prusa3d.com/) is one of the most popular open source 3D printers which consistently ranks among the [best printers](https://all3dp.com/1/best-3d-printer-reviews-top-3d-printers-home-3-d-printer-3d/) money can buy. The printer currently costs about 800. However since many parts have to still be bought from Prusa, it isn't an ideal choice for people living outside Europe or in developing countries. @@ -48,15 +48,11 @@ Preliminary research was carried out to see which open source designs and commer <img src= "https://www.elektrifiziert.net/index.php?attachment/3257-2020-11-18-06h27-57-png/" alt="Voron 2.4" width="500" height="500"> -- [User buildlog](https://www.elektrifiziert.net/forum/index.php?thread/134-voron-2-4-3d-drucker-selbstbau-tagebuch/) +- [Voron buildlog](https://www.elektrifiziert.net/forum/index.php?thread/134-voron-2-4-3d-drucker-selbstbau-tagebuch/) 6. [Hypercube 3D Printer](https://www.thingiverse.com/thing:1752766) is a rigid boxed shape 3D printer made from 2020 aluminium extrusion profiles from user Tech2C and is very popular on the thingiverse website. The design also employs the coreXY mechanism with the attempt to reduce the X-carriage weight. The printer however has a cantilevered bed which causes Z-wobble in prints mainly noticed in printers that have tried to scale the design to a larger build volume. -8. [Hypercube Evolution](https://www.thingiverse.com/thing:2254103) (also known as the HEVO), developed by SCOTT_3D, is an iteration or remix of the HyperCube 3D printer designed by Tech2C. It adds 3030 extrusions around the frame for added thickness, as well as a few more upgrades. It has a decent Wiki as well as a couple of different BOM generators, online and in Excel format. The design comes with configurable CAD files for required build volume and single or double Z axis motors. The build is relatively simple and allows modifications. The design is fully open source i.e. users can use the design, modify it and also use it for commercial purposes. The design is very popular in the community, since it improves on the previous design by tech2C. -6. [Hypercube 3D Printer](https://www.thingiverse.com/thing:1752766) from User Tech2C - - Clear BOM, CAD and Video build log - -7. [Hypercube Evolution](https://www.thingiverse.com/thing:2254103) (also known as the HEVO), developed by SCOTT_3D, is an iteration on the HyperCube 3D printer designed by Tech2C. It adds 3030 extrusions around the frame for added rigidity, as well as a few more upgrades. It has a decent Wiki as well as a couple of different BOM generators, online and in Excel format. The design comes with configurable CAD files for required build volume and single or double Z axis motors. +8. [Hypercube Evolution](https://www.thingiverse.com/thing:2254103) (also known as the HEVO), developed by SCOTT_3D, is an iteration or remix of the HyperCube 3D printer designed by Tech2C. It adds 3030 extrusions around the frame for added thickness, as well as a few more upgrades. It has a decent Wiki as well as a couple of different BOM generators, online and in Excel format. The design comes with configurable CAD files for required build volume and single or double Z axis motors. The build is relatively simple and allows modifications. The design is fully open source i.e. users can use the design, modify it and also use it for commercial purposes. The design is very popular in the community, since it improves on the previous design by tech2C by making it more rigid.  @@ -65,7 +61,7 @@ Preliminary research was carried out to see which open source designs and commer - [Fuson360 Model from User2](https://myhub.autodesk360.com/ue28de06e/g/shares/SH7f1edQT22b515c761e627c356ab003cc8e?viewState=NoIgbgDAdAjCA0IDeAdEAXAngBwKZoC40ARXAZwEsBzAOzXjQEMyzd1C0B2CAEwCY%2BjGADMAtAGYIAI1yiALOMZ9RATjkA2FfIiMe43Ll25xAYzQBfEAF0gA) -8. [Hypercube Evolution Oliver RT or HevORT](https://miragec79.github.io/HevORT/) is a remix **high end** DIY 3D Printer based on the Hypercube Evolution design which can cost about 2000 USD. The printer has auto-levelling of bed using 3 extra z-axis motors. It has a rigid Gantry for achieving high accelerations and speed using a direct drive extruder, whereby the user has achieved a build speed of 500mm/s+ with the printer. +1. [Hypercube Evolution Oliver RT or HevORT](https://miragec79.github.io/HevORT/) is a remix **high end** DIY 3D Printer based on the Hypercube Evolution design which can cost about 2000 USD. The printer has auto-levelling of bed using 3 extra z-axis motors. It has a rigid Gantry for achieving high accelerations and speed using a direct drive extruder, whereby the user has achieved a build speed of 500mm/s+ with the printer. - [Github repository](https://github.com/MirageC79/HevORT) and website has printer configurator, BOM generator and fusion 360 CAD model. <u> **Some Commercial and semi open Source (DIY) Desktop Printers** </u> @@ -78,6 +74,9 @@ Preliminary research was carried out to see which open source designs and commer There are many cheap 3D printer kits that are available these days like the Creality or Tronxy models. These work and do the job but the parts are not optimum or quality components. More often than not users upgrade their cheap printers and end up spending twice as much in the end by replacing components. It is preferrable then to build your own printer from scratch where you get to decide what components you would like to have in the printer. Also if something breaks, you know exactly what to do or how to fix it. + +Great general information and guidelines on building a DIY 3D printer - https://hackaday.com/2016/07/06/build-a-3d-printer-workhorse/ + ## Choosing a 3D Printer for the OLSK The aim of the Open Lab 3D printer is to develop a DIY 3D Printer design that is robust and reliable. It should be possible for anyone to build it, with the posssibility of modifying it according to their budget, requirements and available resources. @@ -174,7 +173,7 @@ According to this [Discussion](https://www.3d-druck-community.de/showthread.php? ### Belts and Pulleys -Most commonly used belts in 3D printers are the GT2 belts which are toothed rubber belts which can have different reinforcing fibes such as steel, fibreglass or just rubber. The GT2 belt is usually 6mm in width and accordingly the pulleys used are GT2 pulleys. The size of the pulleys are specified by the inner bore diameter, the number of teeth and if the pulley is a smooth idler, toothed idler or toothed pulley to connect to a motor for instance. The various forms can be seen below. +Most commonly used belts in 3D printers are the GT2 belts which are toothed rubber belts which can have different reinforcing fibes such as steel, fibreglass or just rubber. The GT2 belt is usually 6mm in width and has a pitch of 2 mm. Accordingly the pulleys used are called GT2 pulleys. The size of the pulleys are specified by the inner bore diameter, the number of teeth and if the pulley is a smooth idler, toothed idler or toothed pulley(i.e. no free bearing inside) to connect to a motor for instance. The various forms can be seen below. 6mm wide rubber GT2 belts are used in the design. According to experience for users of CoreXY printers, here belts with steel reinforcement are to be avoided since these are not elastic enough and so can cause wobbling or misalignment of the idlers. Rather fibre reinforced rubber belts are to be used. @@ -203,15 +202,13 @@ Most commonly used belts in 3D printers are the GT2 belts which are toothed rubb Most common Z-bed autolevelling sensors are reviewed and tested in the following [video](https://www.youtube.com/watch?v=il9bNWn66BY&t=8s), whereby the most simple and precise seem to be the PINDA 8mm inductive sensor from Prusa and the LJ12A3-4-Z/BX inductive sensor. -Inductive sensors are affordable and precise enough for our application and so we will use a 12mm LJ12A3-4-z/BX inductive sensor. This has a 4mm metal detection distance (for ferrous metal like iron) but for non ferrous metals like aluminium this distance can be halved. So the inductive sensor will have to be placed about 2-3mm offset from the nozzle head. +Inductive sensors are affordable and precise enough for our application and so we will use a 12mm LJ12A3-4-z/BX inductive sensor. This has a 4mm metal detection distance (for ferrous metal like iron) but for non ferrous metals like aluminium this distance can be halved. So the inductive sensor will have to be placed about 2 mm offset from the nozzle head. 1. Rasberry Pi for Octoprint (WiFi printing) 2. Fans for cooling electronics - - 6020 Fans for electronics enclosure cooling - - 4020 Duct fan for part cooling - - 5015 Fan for Hotend cooling - -### + - 60mm Fan for Hepa Filter + - 50mm Duct fan for part cooling + - 30mm Fan for Hotend cooling ### **Configuring the MKS Sbase V1.3** @@ -284,35 +281,36 @@ Best Budget Option is the E3D V4 from trianglelabs which prints perfecttly well ### Heated Bed Choice -[Online Calculator](https://jscalc.io/calc/uS8JYjYISgIvzJ1x) to calculate time needed to heat an aluminium or glass build plate with heatbed platform of specific size and power. - -Minimum heatbed power to heat the aluminium build plate to print PLA (70degC) is about - -- use 12AWG wire from PSU>Mosfet and 12AWG Silicon high temp wire from mosfet to heater +A heated bed helps with layer adhesion in part and prevents warping of the part due to rapid cooling. Moreover, most plastics other than PLA cannot be printed without a heated bed. Even PLA prints much better with a 60degC heated bed. PETG for instance with 70degC and ABS with 110 degC. Firstly one must figure out how much power is required for the specific build plate size and material. The following [Online Calculator](https://jscalc.io/calc/uS8JYjYISgIvzJ1x) can be used to calculate time needed to heat an aluminium or glass build plate with heatbed platform of specific size and power. The heated bed is the most power hungry part in a 3D printer build. Therefore the choice of the heated bed directly influences the choice of power supply unit (in terms of power rating). +A solid state relay (SSR) or external MOSFET is often used to switch the bed heater power by connecting its control terminals to the controller board bed heater terminals. An SSR helps by taking the current load away from the controller board and preventing the controller board mosfet from frying, incase of a current surge or high current draw. Make sure that you get the wires to the + and - control terminals of the SSR the right way round. -Bed heater driven using a Solid State Relay -You can use a solid state relay (SSR) to switch the bed heater by connecting its control terminals to the Duet bed heater terminals. Make sure that you get the wires to the + and - control terminals of the SSR the right way round. +Caution: when using a high-powered bed heater, in the event that temperature control fails and the bed heater is turned on at full power for an extended period of time, you should either make sure that the bed heater and bed will not exceed a safe temperature, or else install a thermal cutout to disconnect the bed heater or its power supply before excessive temperatures are reached. This is important since if the SSR fails, it fails in the ON-state and this can lead to the heated bed running without interruption. Here the thermal fuse will break power to the heatbed once the temperature of the heatbed exceeds the thermal fuse specific temperature. -Caution: when using a high-powered bed heater, in the event that temperature control fails and the bed heater is turned on at full power for an extended period of time, you should either make sure that the bed heater and bed will not exceed a safe temperature, or else install a thermal cutout to disconnect the bed heater or its power supply before excessive temperatures are reached. +There are two ways of heating the heatbed 1. via DC power i.e. through the power supply unit or 2. via mains power supply. Below both ways are described along with precautions required. -Mains voltage AC bed heater +#### Mains voltage AC bed heater Use a zero-crossing DC-AC SSR such as Crydom D2425, Kudom KSI240D25-L or Fotek SSR-25DA (note: many Fotek SSRs on sale are fakes, using triacs rated at lower current than the marked rating of the SSR). For 230V bed heaters, SSR-10DA may be sufficient. If your bed heater draws more than about 1/4 of its rated current then the SSR may need a heatsink. Take appropriate safety precautions when using a mains voltage bed heater. In particular: -Connect metal parts of the printer to mains ground. This includes the printer frame, the bed plate if it is conductive (e.g. aluminium), and any other metal parts that the bed heater or SSR wiring might come into contact with if wires break. +- Connect metal parts of the printer to mains ground. This includes the printer frame, the bed plate if it is conductive (e.g. aluminium), and any other metal parts that the bed heater or SSR wiring might come into contact with if wires break. + +- Ensure that it is not possible for the user to touch the SSR terminals or any other exposed mains wiring, or for you to touch the mains wiring when you are working on the printer with power applied. If your SSR is not supplied with a clear plastic safety cover, buy one (for the Crydom SSR listed above, the part number is KS101). -Ensure that it is not possible for the user to touch the SSR terminals or any other exposed mains wiring, or for you to touch the mains wiring when you are working on the printer with power applied. If your SSR is not supplied with a clear plastic safety cover, buy one (for the Crydom SSR listed above, the part number is KS101). +- If the bed is moving, use highly-flexible wire or cable with a sufficient voltage rating to connect the moving bed heater to the stationary wiring. Cable intended for use in multimeter tests leads is one possibility. -If the bed is moving, use highly-flexible wire or cable with a sufficient voltage rating to connect the moving bed heater to the stationary wiring. Cable intended for use in multimeter tests leads is one possibility. +- If the bed is moving, you must use strain relief at both ends of that cable, to reduce the risk of the cable fracturing with repeated movement. -If the bed is moving, you must use strain relief at both ends of that cable, to reduce the risk of the cable fracturing with repeated movement. -If the bed is moving, use a cable chain or similar to make sure that the cable can't get chafed or trapped. +- If the bed is moving, use a cable chain or similar to make sure that the cable can't get chafed or trapped. -Provide a fuse for the bed heater circuit or the whole printer appropriate to the current draw and the current rating of the mains lead. One option is to use a panel mount IEC mains inlet connector with a switch, neon indicator and fuse built in. See http://www.thingiverse.com/thing:965396 for an example setup on a delta printer. +- Provide a fuse for the bed heater circuit or the whole printer appropriate to the current draw and the current rating of the mains lead. One option is to use a panel mount IEC mains inlet connector with a switch, neon indicator and fuse built in. See http://www.thingiverse.com/thing:965396 for an example setup on a delta printer. It is highly recommended that you power the printer via a Ground Fault Current Interruptor (GFCI) - more commonly called a RCD (Residual Current Device) in the UK - to protect against electric shock in the event of a fault. -If in doubt, consult a qualified electrician. +- [Source from Duet3D website](https://duet3d.dozuki.com/Wiki/Choosing_a_bed_heater) + +- Fruitful [discussion](https://forum.duet3d.com/topic/9911/heated-bed-220v-vs-24v/25) on Duet website regarding 24v silicon heater vs AC mains silicon heater + +The following tutorial [video](https://www.youtube.com/watch?v=1VyFejiKkSQ) from youtuber **Teaching Tech**, explains the procedure of installing an AC mains silicon bed heater along with configuring it in Marlin. **Low voltage (12V or 24V) DC bed heater** @@ -320,6 +318,8 @@ Use a low voltage drop DC/DC SSR such as the Auber Instruments MGR-1DD80D100 or If your heater will reach dangerously high temperatures if it is left on at full power, you should always use a TCO to guard against electronics or firmware failure. The alternative is to choose the heater power carefully so that it is powerful enough to reach the temperatures you want quickly, but not so powerful as to reach a dangerously high temperature when left fully on for a long time. +- use 12AWG wire from PSU>Mosfet and 12AWG Silicon high temp wire from mosfet to heater + ### Choosing Power Supply [Info](http://customize-3d.com/how-to-calculate-power-requirements-of-3d-printer-safeguard-controller.html) @@ -335,8 +335,7 @@ To get the amperage, simply divide by the output voltage, e.g. 360W / 12V = 30A. Here are some examples: - The standard minimum for 3D printers is usually 240 watts (12 volts @ 20 amps). That would be enough for a printer with a single hot end and a heated bed around 180 x 180 mm. -- With a 200 x 200 mm bed or a second hot end, you’d be better off with 300 watts (12V @ 25A). -With both a second hot end and a 200 x 200 mm heated bed, or single extruder with up to a 300 x 300 mm heated bed, 360 watts are standard (12V @ 30A). +- With a 200 x 200 mm bed or a second hot end, you’d be better off with 300 watts (12V @ 25A). With both a second hot end and a 200 x 200 mm heated bed, or single extruder with up to a 300 x 300 mm heated bed, 360 watts are standard (12V @ 30A). - With anything larger than that, a power supply rated upwards of 400W would be recommended. With a 24V PSU, the rules change slightly, as you don’t need quite as much current. Still, we would recommend sticking to the above standard for the best possible operation. @@ -362,26 +361,24 @@ https://all3dp.com/2/3d-printer-power-supply-how-to-choose-the-right-one/ ### 3D printer Wiring -One of the most important things about your 3D Printer is the Wiring. If the wire gauge is too small you won’t get enough current to your parts and can even lead to busted cables. Too large of a gauge and you might have a problem fitting those crimped terminals into the connectors. +One of the most important things about your 3D Printer is the Wiring. If the wire gauge is too small you won’t get enough current to your parts and can even lead to busted cables. Too large of a gauge and you might have a problem fitting those crimped terminals into the connectors. So, the first thing to look for in a wire type is a stranded wire. The reason being your printer will create thousands of cycled movements and if your wire is a solid it will be susceptible to break over the duration of repeated abuse. The stranded wire allows for the cable to flex and move without breaking over time. -So, the first thing to look for in a wire type is a stranded wire. The reason being your printer will create thousands of cycled movements and if your wire is a solid it will be susceptible to break over the duration of repeated abuse. The stranded wire allows for the cable to flex and move without breaking over time. +A few useful tips: Depending on your level of expertise it may be useful to practice crimping and soldering before wiring everything up. Bad crimps are a major source of problems later on an sometimes hard to identify! Safety Mains cables should be properly dimensioned. Use at least 20 AWG for mains connections, even better would be 18 AWG. Buy a quality SSR, do not source one from china or your house will catch on fire (see Official Sourcing Sheet)! Add a 115-125°C thermofuse to your bed heater as an additional safety measure. Dont run your bed above 105°C, this greatly reduces the lifespan of the adhesive holding it onto the build plate Connect ground to your bed! Connect a ground to your frame! -The RepRap Wiki page recommends using 22AWG or 20AWG +Connectors The recommended MicroFit 3.0 connectors are specced up to 5A and should be used for all connections to the stepper motors, hotend and limit switches The dupont connectors are used for connections to the RAMPS board Adding molex connectors to all stepper motors is useful. You can disconnect motors while moving the gantry manually to avoid damage to the RAMPS board. Use a 3pin MLX connector (see the official sourcing guide) to allow your bed to be removable without disconnecting from the SSR directly. The thermistor can use a 2pin microfit connector. +Cables The specced silicone wire has been chosen because: It is very high strand count, which means it has higher fatigue life Silicone insulation withstands heat and is more flexible which is good in high movement applications It is less prone to snagging on other wires or the walls inside the cable chain Check you cable loom before installing the tape chains. You need at least: 8x 24AWG wires in the z chain (2 steppers) 4x 24AWG wires in the y chain (endstops) 7x 24AWG (probe, fans, thermistor) 2x 20AWG in the x chain (heater) - do not downsize these, they are oversized for safety reasons +[SOURCE from VoronDEV website](https://www.voron.dev/home/voron-2-2-supplement/electronics) [Instructions](http://www.hobbycncaustralia.com.au/Instructions/iI1powerchassis.htm) on setting up the power connector. - -  **Points to be noted** The hot end and thermister wires are not polarity dependent so the + and - can be plugged in anyway. -From top left, the motors will be connected in the order of X, Y, Z followed by the extruder motor. For the Z axis a splitter will have to be used to join both the Z-axis motors to a single Z port. - -#### **3D Printer Wiring Connectors** +### **3D Printer Wiring Connectors** **Dupont Connectors** @@ -389,6 +386,8 @@ These connectors work great for RAMPS and Rumba type controller boards with open  +**JST Connectors** + The JST connectors are what are used on the 32 bi boards such as the MKS, AZteeg etc. 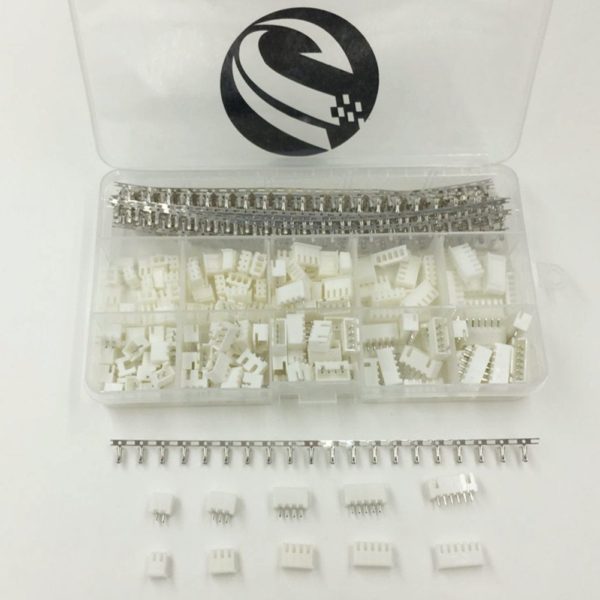 @@ -421,29 +420,81 @@ The compiling of the Marlin configuration can be done using visual studio. The P Open the **platformio.ini** file in the **marlin-2.0.x** folder and change the **'default_envs'** variable of the default atmel to LPC1768. This is the CPU on the MKS Sbase V1.3, and needs to be defined here. Save and exit the platformio.ini file. --- +Before You Begin to get your core **Configuration.h** settings right you’ll need to know the following things about your printer: + +- Printer style, such as Cartesian, Delta, CoreXY, or SCARA +- Driver board, such as RAMPS, RUMBA, Teensy, etc. +- Number of extruders +- Steps-per-mm for XYZ axes and extruders (can be tuned later) + - These can be calculated easily using Prusa's Online [Calculater](https://blog.prusaprinters.org/calculator_3416/) +- Endstop positions +- Thermistors and/or thermocouples +- Probes and probing settings +- LCD controller brand and model +- Add-ons and custom components +More Information on how to change the configuration according to your setup can be found on Marlin's Configuration page. [Source](https://marlinfw.org/docs/configuration/configuration.html) + Next Open the file **Configuration.h** with the file path - Marlin-2.0.x > Marlin > Configuration.h. Here the first thing to define is the motherboard used i.e. here after #define MOTHERBOARD enter **BOARD_MKS_SBASE** as seen in the code snippet below. -Next basic settings such as: - - Type of electronics - - Type of temperature sensor - - Printer geometry - - Endstop configuration - - LCD controller - - Extra features - - - Advanced settings can be found in Configuration_adv.h + - More advanced settings can be found in Configuration_adv.h +### Defining Motherboard type // Choose the name from boards.h that matches your setup #ifndef MOTHERBOARD #define **MOTHERBOARD BOARD_MKS_SBASE** #endif ---- -Next for an NPN NO inductive probe like the set Z_endstop +### Setting Stepper Steps + +Considering we are using a GT2 belt of (i.e. distance between two teeth) pitch 2mm and our pulleys have 20 teeth. Therefore distance covered with one full revolution of the 20T pulley will be 40mm. Given that we have 1.8deg stepper motors, i.e. each step of the stepper. This means one full revolution of 360 degrees will be covered in 360deg/(1.8deg) = 200 steps for one full revolution. Considering we have default 1/16 microstepping as default on the MKS Sbase board i.e. each step will be further broken down into 16 steps. This means we will have 16 * 200 = 3200 steps for each revolution. + +Calculating Steps/mm = Total Steps / Total distance per Rev + = 3200 / 40 + = 80 Steps/mm + +The value of 80 can be input then for the X and Y steps/mm in Marlin. + +For the Z axis we have a lead screw which has a pitch of 8mm and a lead of 8mm. This means each revolution moves the lead screw nut 8 mm. Assuming again 3200 steps per revolution - this gives Steps/mm to be 3200/8 = 400 Steps/mm for Z axis motor. + +For the extruder motor, first tryout is with an MK8 extruder fixed to frame (bowden setup), for which this [website](https://gulfcoast-robotics.com/pages/mk8-aluminum-extruder-assembly-guide#:~:text=It%20will%20be%203200%20%2F%2034.38mm%20%3D%2093%20steps%20per%20mm.) shows the extruder steps calculation along with assembly steps for the MK8 extruder. This gives the value to be 93 steps/mm which can be further fine tunner by running some tests according to this [video](https://www.youtube.com/watch?v=r_L79WqHegQ) + +A sherpa mini direct drive extruder which is a fully open source design for a lightweight direct drive extruder, has been ordered which once assembled will be calibrated accordingly and setup on machine. But for now, the MK8 bowden drive will be tested first. + +### Configuring Extruder Steps + +[This](https://www.youtube.com/watch?v=r_L79WqHegQ) is a useful video tutorial on how to calibrate or set the extruder steps in Marlin for a bowden drive (MK8 extruder here). + +### Configuring NPN NO 12mm inductive probe + +An inductive probe can be attached to the Z-min Endstop pins in the controller board to use autobed levelling. + +Useful [video](https://www.youtube.com/watch?v=EcGFLwj0pnA) describing setting up an NPN NO inductive probe and levelling the Z-probe manually using Repetier Host. + +The inductive probe wires will be attached to the Z-min endstop port which has three pins namely V(voltage), S (Signal) and G (Ground). If the inductive probe is a 5V probe, it can be connected directly to the Z-min Endstop. However, if the NPN NO or NC inductive probe is rated 6-36V or 10-30V, it cannot be connected directly to the Z-min Endstop since the 5V from the Z-min Endstop V pin will not be sufficient to power the probe. The probe will then have to be powered with full 24V from the PSU. Consequently, the output signal from the sensor to board will be have the same voltage as the input signal and as our board is rated 24V, it powers the sensor with 24v and therefore the output signal will also have 24v. This could fry the Signal pins on the Z-minstop connector if not reduced since they are rated for a maximum of 5V. This can be done in two ways: +1. Using a resistor divider setup to reduce the voltage across the G and S pins to be less than 5V +2. Using a transistor + +The voltage divider setup does not work since the pullup resistors within the MKS Sbase V1.3 board cannot be deavtivated through the firmware. The transistor method however works. The following [page](https://snafu.priv.at/interests/tinkering/probe_sbase.html) explains the method to attach the transistor to the NPN NO probe. + +### Wiring a mechanical EndStop + +A mechanical endstop was wired according to the Simple setup shown . Whereby the C pin on endstop was connected to signal pin on Y-min Endstop and NC pin was connected to Ground pin on Y-min endstop on controller board. This creates a normally closed Y endstop. A mechanical endstop was used since all the optical endstops turned out defective. + +[Tutorial video on connecting a mechanical endstop](https://www.youtube.com/watch?v=fKyn02Ntz7A) + +### Connecting LEDs + +Good video explanining different methods to connect [LEDs](https://www.youtube.com/watch?v=ONyxRprg-Ag) + +### Setting motor current in Marlin + +Motor current can be defined in config_adv.h file whereby the digipot option needs to be enabled. Due to a software bug marlin does not configure. The following fix needs to be made as seen [here](https://github.com/MarlinFirmware/Marlin/commit/29356e390323ed4d405e520ad3d4d2b7efcff008) +### Initial Bed Levelling +Even though the milled aluminium build plate is flat, it sits on 3D printed brackets and so the bed will not sit on a completely flat plane. Therefore, the build platform needs to be levelled by adjusting the levelling screws. This process is well explained in the following [article](https://all3dp.com/2/3d-printer-bed-leveling-step-by-step-tutorial/). ## Calibration & Fine Tuning Methods diff --git a/docs/machines/DesktopLaserCutter.md b/docs/machines/DesktopLaserCutter.md index b0c5dd7..ce3d6e4 100644 --- a/docs/machines/DesktopLaserCutter.md +++ b/docs/machines/DesktopLaserCutter.md @@ -1 +1,7 @@ -# Desktop Laser Cutter \ No newline at end of file +# Desktop Laser Cutter + +[DIY Laser Cutter Fume Extractor](https://www.instructables.com/Build-a-laser-cutter-fume-extractor/) + +1. LaserDUO - Daniele Ingrassia +2. Lasermini - Daniele Ingrassia +3. \ No newline at end of file diff --git a/docs/machines/LargeFormatCNCRouter.md b/docs/machines/LargeFormatCNCRouter.md index bb8decb..df69904 100644 --- a/docs/machines/LargeFormatCNCRouter.md +++ b/docs/machines/LargeFormatCNCRouter.md @@ -1,6 +1,6 @@ # Large Format CNC Router -1) [PrintNC](https://wiki.printnc.info/en/home) Large CNC Router - Fully Open Source CNC Router build with great Wiki having full assembly instructions +1. [PrintNC](https://wiki.printnc.info/en/home) Large CNC Router - Fully Open Source CNC Router build with great Wiki having full assembly instructions - Complete BOM, CAD and instructions to build. 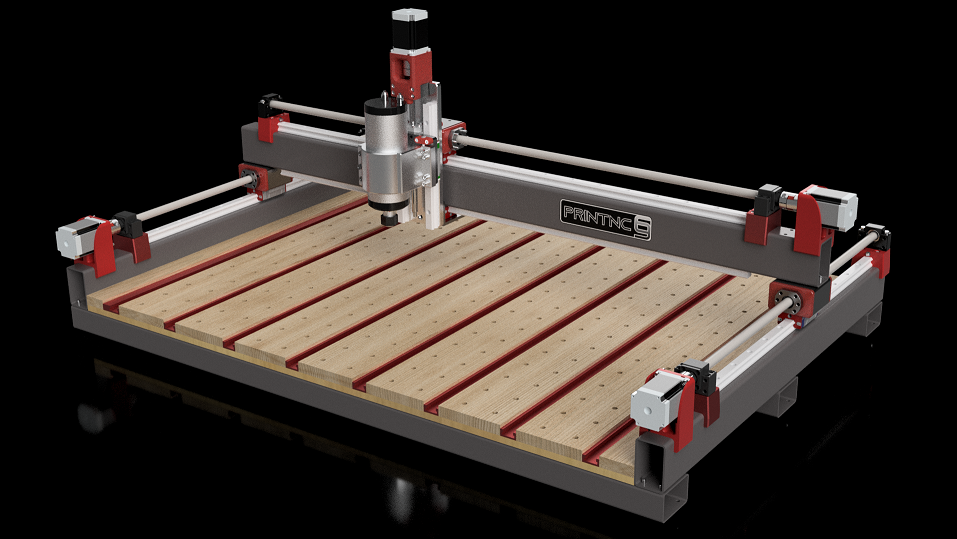 Specifications: @@ -10,5 +10,58 @@ Specifications: - VFD water cooled spindle - GRBL -2) 3D printer CNC Rounter from [TopsCNC](https://createforcuriosity.com/fr/design/4A8e0Mgv/details) is an open source CNC router design with all fittings 3D printed. -- \ No newline at end of file +2. 3D printer CNC Rounter from [TopsCNC](https://createforcuriosity.com/fr/design/4A8e0Mgv/details) is an open source CNC router design with all fittings 3D printed. + + +3. Mekanika Website: https://www.mekanika.io/build + +4. MechMate CNC plans cost 100 USD : http://www.cvsupply.com/mechmate-cnc-router.html + - PDF build drawings and forum support. + +5. DIY CNC Router from youtuber sbirdranch with full CAD sketchup file and partial BOM with video build guide: + - https://www.youtube.com/watch?v=gg2UvbRsLP0&feature=emb_rel_pause + +6. Large Format CNC Router from Arachne.net – + - His Grabcad model: https://grabcad.com/library/large-format-cnc-frame-3d-printer-frame-1 + - His Website with pdf plans: https://arachne.net/large-format-cnc-frame-1-4/ + - BOM, CAD and PDF drawings for assembly. + +7. Simple CNC or plasma build with steel profiles - http://goodenoughcnc.eu/hybrid-cnc/ + - BOM, CAD and build instructions + +8. Website for mom-fablab.fr’s CNC Router machine - https://www.mon-fablab.fr/openmakermachinepro/ressources/le_wiki + - BOM, CAD and good build instructions. + - Outer dimensions: 1300x1500mm + - Clamping area: 1500x1198mm + - Working area : 870x1050 + - Z axis : 230 mm + - Spindel : KRESS 1000W + - Ball screw spindles + - Nema 23 + industrials steppers + - License GPLv3 + +9. Uncle Phil’s Volk Fraese – DIY build with CAD and Youtube video build instructions in german - https://www.unclephil.de/volksfräse-vf1/ + - Youtube build guide: https://www.youtube.com/watch?v=pT0H5iz9QX8&list=PLANYX4gwa2XsMHxZewXTkMipJeNGa3MbG + - High Power CNC for Thick Aluminium/Steel + +10. CNC Mill from Kris Temmerman +- Youtube build video: https://www.youtube.com/watch?v=q0RE-h1VDIg +- Incomplete CAD file: https://a360.co/2NCSX05 + +11. Lukas Goessler from Austria: + - His Website: https://lukasgoessler.wixsite.com/goezzlers + - His Grabcad Profile: https://grabcad.com/lukas.gossler-2 + - His Youtube Profile: https://www.youtube.com/channel/UCcfWtHeqCce18_PdMPOpbIQ + - Parts: bt30 spindle and servos are bought an aliexpress 35mm rails (Hiwin) + 25mm ballscrews /5mm pitch (ISEL) bought with a local supplier. Flat grounded plates: came from misumi controler: edingcnc iCNC600 + +12. Fixed gantry DIY Build from youtuber ‘This Old Tony’ + - 3 part build video on youtube: https://www.youtube.com/watch?v=K9UA9ZRFwWU + - CAD file (Incomplete – good for reference) - https://drive.google.com/file/d/0BziGqMVEh_qrdlBGTmRKcThVRDg/view + +13. Homemade Steel Frame CNC Router ‘The Ferrous CNC’ for Wood, Acrylic and PCBs + - Youtube Build guide: https://www.youtube.com/watch?v=vtPmPFdVZ4g + - BOM, CAD and build Plans: https://whitman.tech/ferrouscnc/ + - Cost: 3000 USD + +14. Rock Solid CNC from Dr. Robert + - \ No newline at end of file diff --git a/docs/machines/LargeScale3DPrinter.md b/docs/machines/LargeScale3DPrinter.md index a0816e0..61b20fe 100644 --- a/docs/machines/LargeScale3DPrinter.md +++ b/docs/machines/LargeScale3DPrinter.md @@ -1 +1,8 @@ -# Large Scale 3D Printer \ No newline at end of file +# Large Scale 3D Printer + +1. BigFDM printer by Daniele Ingrassia + - CAD, BOM and Instructions (beings made) +2. Giant 3D Printer by youtuber Ivan Miranda - https://www.youtube.com/watch?v=albFKmWW4nA + - CAD, BOM and youtube build guide available +3. Large Desktop 3D printer build video from Ivan Miranda https://www.youtube.com/watch?v=c9XG4z0Y8m8 +a. Shows various build and assembly methods diff --git a/docs/machines/Plasma Cutter.md b/docs/machines/Plasma Cutter.md index d0dc293..c61ce2b 100644 --- a/docs/machines/Plasma Cutter.md +++ b/docs/machines/Plasma Cutter.md @@ -1,3 +1,29 @@ # Open Source Plasma Cutter Designs -1. [Office Plasma Cutter](https://www.thingiverse.com/thing:3645035) from thingyverse user DerM4209 +1. 2 Part DIY Plasma Cutter [Build](https://www.youtube.com/watch?v=LvxOBvpgalY) + +2. [Full CNC Plasma Build](https://www.youtube.com/watch?v=lP2-2duBYBM&list=PL9xPdBFt5g3Q6TkuhhfQmQNm6TdvNkPuX) + +3. Plasma CNC Build with explanations but no CAD or frame build - https://www.youtube.com/watch?v=OkVC4EAEPdQ + +4. Stefan Cymbalak CNC Plasma Cutter Video Build Guide - https://www.youtube.com/watch?v=x1uTFj38Pso&list=RDCMUC5WIpuhb1Bf761Oa-JslZCQ&index=3 +a. BOM available on Youtube Video Description +b. CAD Model to buy - https://www.etsy.com/listing/942110597/4x4-cnc-plasma-table?ref=search_recently_viewed-4 + +5. Big size CNC plasma Cutter design on ETSY (Plans cost 54 Euros) +a. (2500x1250) CNC Plasma with milling option for DIY - https://www.etsy.com/listing/925312655/digital-project-big-size-2500x1250-cnc?ref=search_srv-5 + +6. Custom CNC plasma cutter from youtuber Optimal Welding: https://www.youtube.com/watch?v=RcUxoCZ0VbE +a. No CAD, BOM but just a mediocre video build guide +b. Video has information of build design however for linear guides + +7. DIY CNC Plasma cutter low cost with BOM and CAD on grabcad: +a. https://grabcad.com/library/inexpensive-budget-cnc-plasma-table-1 + +8. CNC Plasma cutter with good concept of Motor mount + Belt drive (with tensioner): https://grabcad.com/library/cnc-plasma-cutter-concept-idea-1 + +9. CNC Plasma table with full build instructions – CAD and BOM https://grabcad.com/library/cnc-plasma-with-plans-and-building-instructions-1 + +10. Commerial DIY CNC Plasmacutter (From CNC Router Parts) build with good ideas on how to design table: https://www.youtube.com/watch?v=ugjJXa6Sfl0 + +11. [Office Plasma Cutter](https://www.thingiverse.com/thing:3645035) from thingyverse user DerM4209 -- GitLab