diff --git a/docs/CE Certification/Information.md b/docs/CE Certification/Information.md new file mode 100644 index 0000000000000000000000000000000000000000..f316de356a09f643a6880a53319ef09130147884 --- /dev/null +++ b/docs/CE Certification/Information.md @@ -0,0 +1,29 @@ +# CE Certificaiton of Open Source hardware + +## What is CE Certification? + +write on +- What does it means when a product is CE certified? +- Who can CE certify + +## 6 Steps for CE certification + +1. Identify which directives are applicable for each module: Not all products required to be CE certified so we need to check each of our modules to fall in at least one CE marking directive. If not, no CE marking is needed. +2. Identify the applicable requirements of the applicable directives: Each directive has it’s own methods of demonstrating conformity. This usually depends on the classification of the product and its intended use. +3. Every directive has a number of essential requirements which the product has to meet. +4. Identify the route to conformity: The CE marking process is always a self-declaration process however it can be required to involve a third party. This is described in the “system of attestation†and will vary between directives. +5. Assessment of the product’s conformity: When all the requirements have been met, you need evidence that the product meets the essential requirements of the directive(s) +6. Compile the technical documentation: This information should cover every aspect relating to conformity and should include design, development and manufacture of the product. +7. Make a declaration and affix the CE mark: When the product satisfies the applicable CE marking directives as they must complete a declaration. +[Source, Last accessed 25/08/2021](https://www.openmotics.com/en/how-to-make-open-source-hardware-products-ce-certified/) + +When there is no CE marking directive, then the [General Product Safety Directive](https://ec.europa.eu/info/business-economy-euro/product-safety-and-requirements/product-safety/consumer-product-safety_en) applies. + +---- + +Further Points to elaborate: + +1. Points to consider for the general product safety directive during design phase +2. Check which machine directives to consider for the various machines - Possible further info available in the thesis done by Tobias's student +3. Divide the points in the various categories such as mechanics and drive, user safety features, electronics etc. +4. Make guidelines for the design to be considered so that the machines can be CE certified without further steps. \ No newline at end of file diff --git a/docs/electronics/Heated Bed.md b/docs/electronics/Heated Bed.md deleted file mode 100644 index fd978ab3b4879b5c82e3a40d158d51057d9cafe0..0000000000000000000000000000000000000000 --- a/docs/electronics/Heated Bed.md +++ /dev/null @@ -1,49 +0,0 @@ -# Home -## Introduction : ----- -Heat beds are used because they dramatically improve print quality by keeping the extruded plastic warm and thus preventing warping. Heat beds work to prevent this warping effect by keeping your part warm during the whole printing process which keeps the material at or above heat-deflection temperature (the temperature at which it is malleable). Keeping the parts in the heat-deflection range ensures that the part remains flat on the print bed. - -## Types of Heat Bed: ------ -Heated beds usually yield higher quality finished builds with materials such as ABS and PLA. Regardless of the heat bed you are using, you should generally use these temperatures (heat deflection points) for [PLA and ABS](http://bootsindustries.com/heat-bed-3d-printing/): -1. For PLA 50-60°C -2. For ABS 100-110°C - -### Heated Beds Using PCBs as Heating Element: ----- -[We recommend the PCB heat bed]( http://bootsindustries.com/heat-bed-3d-printing/) as the heating elements. These are available with the budget 3D printers. However, these won’t last long if your 3D printing projects are complex and require frequent jobs with 3D printers. In short, they are meant for smaller projects that do not take much longer to complete. -### Recommended PCB HEAT BED: ----- -• The [MK2A heat bed (200mm x 200mm)](https://www.amazon.de/-/en/MK2-a-heated-bed-300-x-200-mm/dp/B01NBEX91J) is a good example of a PCB heat bed. These heat beds are used by many 3D printers due to their great performance and affordability. - -• This particular heat bed has 2 integrated LEDs and an integrated resistor which makes it rather ‘plug and play’ when compared to other solutions. - -#### Electrical Construction : - -There are pads and un-plated through holes for connecting the power wires. Ensure that the wire you use is thick enough for 10A, and solder it to the pads on the track side of the PCB. It is a good idea to think about strain relief so your moving build platform does not flex the joint, this can lead to failure of the joint over time. It is recommended routing the wire from the heated bed to strain relief on the thick sheet before routing it to your controller/power supply. - - - -The pads to solder onto have been greatly increased as shown in the picture above. The picture shows the wires prepared for soldering routed through the holes for extra security. This does not remove the need to use proper strain relief. - -#### Dual Power version: - -[MK3 ALU-Heatbed Dual Power](https://www.robotdigg.com/product/202/MK3-Dual-Power-ALU-Heatbed) have features similar to MK2 and you can also operate this board with 12V or 24V. Running 24V on the 12V terminals will heatup the heatbed to 100 degree in only 2 minutes (Your printer controller will regulate the power to the heatbed in order to get your preset temperature. - - -When connecting the heatbed in the 12V setting it is important that you connect solder pad 2 and 3 directly on the heatbed - - - - - -### Electronics Design: ------ -* To power the bed, you should use a PC PSU or universal power supply that can output at least 10A @ 12V. -You may be able to get universal laptop-PSUs with adjustable voltage for a range of [15-24V at 80-180W](https://reprap.org/wiki/Heated_Bed#Electronics_Design_.231). - -* The heating elements can be nichrome wire, power resistors for higher temperatures or ready-made, flat heating-pads for lower temperatures. -* nichrome wire is cheaper and takes less space then power resistors. -* [This design uses a simple analog control circuit and is easy and cheap to build (20$US for the electronics)](https://reprap.org/wiki/Heated_Bed#Electronics_Design_.232). - - diff --git a/docs/electronics/Sensors.md b/docs/electronics/Sensors.md index dfd5be57068a2b72559beafd450d19e38f84b087..bc82dc41636297fe667a920925a724c6cec3a16c 100644 --- a/docs/electronics/Sensors.md +++ b/docs/electronics/Sensors.md @@ -1,5 +1,6 @@ -# Special Feature Of CNC Machines -## Introduction: +# Home + +# Sensors --- A process monitoring **Sensor** groups, expertise library, and neural network to automatically determine and correct process parameters such as cutting speed, depth and rate. Certainly, intelligent CNC machines also have motion control units that include **position sensors, rotary encoders, proximity switches, current sensors and pressure sensors** to work with process monitoring sensor group and achieve powerful function diff --git a/docs/electronics/Servo Motors.md b/docs/electronics/Servo Motors.md deleted file mode 100644 index e69de29bb2d1d6434b8b29ae775ad8c2e48c5391..0000000000000000000000000000000000000000 diff --git a/docs/electronics/Stepper Drivers.md b/docs/electronics/Stepper Drivers.md deleted file mode 100644 index bc03a82c28885241c861c21017044e781c9ae0a1..0000000000000000000000000000000000000000 --- a/docs/electronics/Stepper Drivers.md +++ /dev/null @@ -1,72 +0,0 @@ -# Home - -## Introduction ---- -Stepper motor drivers are specifically designed to drive stepper motors, which are capable of continuous rotation with precise position control, even without a feedback system. The usual stepper motor drivers offer adjustable current control and multiple step resolutions, and they feature built-in translators that allow a stepper motor to be controlled with simple step and direction inputs. These modules are generally basic carrier boards for a variety of stepper motor driver ICs that offer low-level interfaces like inputs for directly initiating each step. - - -## Types of Stepper Drivers ---- -There are different types of stepper motor drivers. Here are the three main versions that you will come across- - -- **L/R Stepper Motor Driver** : This type of stepper motor driver carried out rotations at a low to medium speed and this can result in fairly limited ranges of power output. They can still offer a full rotation but they don’t usually offer control in regards to variable current levels. - -- **Chopper Stepper Motor Driver – Micro-step** : These types of stepper motor drivers are able to use a micro step mode. This means that it runs smoother and more efficiently as the current rate is regulated at all speeds. It works on a solitary supply of high voltage and has output transistors that have come on and off automatically. - -- **Bi-level Stepper Motor Driver**: -The third type of stepper motor driver is the bi-level and this can use both high and low-level voltages. It works by powering up to a high rate of current and when it reaches the level that you need, the high voltage is turned off. The low voltage is then used to maintain this level of supply when it is in use. - - -### Specifying stepper drives : ---- - -- select a stepper with at least twice as much torque as required at the target operating speed, and use a motor rated at about ¼ supply voltage. - - The driver should output at least 1.4 times the motor's rated current. Choose a driver that has several step resolutions to test different microstepping settings to get the smoothest motion. Finally, make sure the driver can receive enough step pulses to rotate your motor at the desired speed. Sometimes drivers are limited to something small like 10 kHz. If you're hoping to microstep even at **8× with a 1.8° stepper**, your maximum revolutions per sec speed is **10,000/(8 × 200) = 6.25 rps**. - - To make a stepper motor run, we need to use possibly a A4988 or possibly a DRV8825 or possibly a Trinamic TMC2130. - - - -### Best CNC Stepper Motor Drivers for Every CNC Application: ---- - -Here are the best Stepper Drivers available today [2021] for CNC applications: - -- **SongHe DRV8825 Stepper Motor Driver** **(Recommended)** : This CNC motor controller can run a 1.5 A NEMA 17 motor reasonably well and obviously any stepper motor that's smaller than that. While the A4988 can do up to 1/16 microstepping, the DRV8825 can do up to 1/32 microstepping, making the motor movement smoother. The Songhe DRV8825 ships with aluminium heat sinks included. -Adjusting the current from the driver in DRV8825 is very similar to that of the A4988, by doing a potentiometer adjustment. - -- **StepperOnline DM542T Stepper Motor Driver** : This stepper driver can power almost any NEMA 17 and NEMA 23 motor, except probably the high torque NEMA 23 with 4.2A. the driver an excellent choice for almost any GRBL based DIY CNC project, including the large 8' x 4' frames. The heat sinking and cooling on this motor is excellent. It is a very silent driver and it doesn't sweat even when you hit 4A. - -- **GECKO G540 4-AXIS Stepper Motor Driver**: One important difference between the G540 and the other steppers is that it is run on Mach3/4 and LinuxCNC instead of GRBL and operates via a parallel port to connect to the CNC controller. - - - -### Other Commercial Stepper Drivers - ---- - -one of these has the potentiality to suit our needs: - -- **ULN2003 Driver Board** : a great choice for someone looking for a driver that is less phase specific. - -- **DevMo Stepper Motor Driver** : a great choice for anyone concerned about the heat levels produced from their 3D printer. The driver operates at 4.75 Volts and 28 DC. The Devo model runs at a temperature of 70 degrees. - -- **Bolsen Stepper Driver** : A Voltage of 35 with 2A output drive capacity, great choice for someone with a single-phase 3D printer. - -- **ARCELI A4988 Compatible Stepper** : the best model to use if you’re looking to make your machine faster in speed. It is compatible with multiple 3D printer voltages, ranging from 6V to 36V 2.5A. - -- **SMAKN TB6600 Upgraded Version** : A phase flow driver that is H-bridge bipolar constant. A maximum output current of 4.0A. The driver can be made to produce an output current of 8.0 A. The power supply chip version comes with a five-year warranty. - -- **SparkFun EasyDriver** : you’re looking for a driver with many adjustabilities but no real mechanism for heat control. - -- **Gikfun EasyDriver Shield Stepper Motor Driver for Arduino** : It is compatible with multiple stepper motors that come on a variety of voltage. Any four, six, and eight stepper motors should be able to use this driver. It is an A3967 micro-stepping driver - -- **HobbyPower Stepstick 4-layer DRV8825** : the best choice for those looking for the **most micro-step resolutions** for their 3D printer.It is known for being well suited for those who like to build their 3D printers or have other do-it-yourself inclination. - -- **DaFuRui 5-piece A4988 Stepstick Driver** : A translator is built into the complete micro-stepping motor driver frame that allows for the stepper motor’s easy operation. A great option if you want a driver that’ll fit in more than just your 3D printer. - -- **BIGTREETECH Direct TMC2209 UART driver** : a high tech motor drive that comes with a lot of extra mechanisms and most expensive one. - -- **Tongbay TMC2208 V3.0 Stepper Motor Driver** : A single UART wire that is used for advanced configurations. It is a more high tech motor with lots of extra advancements. - - - diff --git a/docs/electronics/Stepper Motors (3D Printers).md b/docs/electronics/Stepper Motors (3D Printers).md deleted file mode 100644 index 6c2893009654d4303f002940be01295db76d9214..0000000000000000000000000000000000000000 --- a/docs/electronics/Stepper Motors (3D Printers).md +++ /dev/null @@ -1,82 +0,0 @@ -# Understanding Stepper Motor Specifications ---- - -## Bipolar Stepper Motor ---- -- A bipolar stepper motor has an onboard driver that uses an H bridge circuit to reverse the current flow through the phases. By energising the phases while alternating the polarity, all the coils can be put to work turning the motor. - -- In practical terms, this means that the coil windings are better utilised in a bipolar than a standard unipolar stepper motor (which only uses 50% of the wire coils at any one time), making bipolar stepper motors more powerful and efficient to run. - -- The trade-off is that they’re usually more expensive initially than standard unipolar versions, because unipolar stepper motors don’t require the current flow to be reversed in order to perform stepping functions - this makes their internal electronics much simpler and cheaper to produce. - -> So, we must use the bipolar stepper motors. - -## Rated Current ---- -- This is the maximum current we may pass through both windings at the same time. The maximum current through one winding (which is what really matters when using microstepping) is rarely quoted and will be a little higher. However, even with one winding driven at the quoted rated current, the motor will get very hot. - -- The usual practice is to set the motor current to no more than about 85% of the rated current. Therefore, to get maximum torque out of the stepper motors without overheating them, we should choose motors with a current rating no more than 25% higher than the recommended maximum stepper driver current. - -> **MKS SBASE V1.3** uses the **DRV8825** stepper motor controller IC. The provides 2.5 A maximum drive current at 24 V. Considering half of the maximum drive current (1.25 A) at 12 V, to get maximum torque out of the motors without overheating them, we should choose motors with a current rating around 1.56 A (25% higher than 1.25 A). - -## Holding torque ---- -- This is the maximum torque that the motor can provide with both windings energised at full current before it starts jumping steps.The holding torque with one winding energised at the rated current is about ***1/sqrt(2)*** times that. - -- The torque is proportional to current (except at very low currents), so for example if we set the drivers to 85% of the motor rated current, then the maximum torque will be ***85% * 0.707 = 60%*** of the specified holding torque. - -- ***Rated current comparison***: 85% of 0.4 A rated current = 0.34 A, 85% of 1.8 A rated current = 1.53 A. -- ***Holding torque comparison***: 60% of 40 Ncm = 24 Ncm, 60% of 50 Ncm = 30 Ncm. - -> So, choosing the motor having 1.8 A rated current and setting the drivers at 1.53 A, we can get maximum torque of 30 Ncm (60%) out of the motors without overheating them. - -## Step angle ---- -- There are two common step angles: 0.9 and 1.8 degrees per full step, corresponding to 400 and 200 steps/revolution. - -- 0.9 deg motors have slightly lower holding torque than similar 1.8 deg motors from the same manufacturer. - -> Most 3D printers use 1.8 deg/step motors. - -## Resistance and rated voltage ---- -- These are simply the resistance per phase, and the voltage drop across each phase when the motor is stationary and the phase is passing its rated current (which is the product of the resistance and the rated current). - -- These are unimportant, except that the rated voltage should be well below the power supply voltage to the stepper driver. - -> The 0.4 A stepper motor has the rated phase voltage of 12 V (phase resistance_30 ohms * rated current per phase_0.4 A). Providing 12 V supply voltage to the **DRV8825** stepper motor controller IC, we must use the 1.8 A rated current stepper motor. Because it has the rated phase voltage of 2.7 V (phase resistance_1.5 ohms * rated current per phase_1.8 A), which is much lower than the supply voltage (12 V) compared to the 0.4 A stepper motor. - -## Inductance ---- - -- The inductance of the motor affects how fast the stepper motor driver can drive the motor before the torque drops off. If we temporarily ignore the back emf due to rotation and the rated motor voltage is much less than the driver supply voltage, then the maximum revs/second before torque drops off is: - -> ***revs_per_second = (2 * supply_voltage)/(steps_per_rev * pi * inductance * current)*** - -- If the motor is driving a GT2 belt via a pulley, this gives the maximum speed in mm/sec as: - -> ***speed = (4 * pulley_teeth * supply_voltage)/(steps_per_rev * pi * inductance * current)*** - -- **Example**: a 1.8 deg/step (i.e. 200 steps/rev) motor with 3.2 mH inductance run at 1.5 A using a 12 V supply, and driving a GT2 belt with 20 tooth pulley would start losing torque at about 318 mm/sec. This is the belt speed, which on a CoreXY or delta printer is not the same as the head speed. - -- In practice the torque will drop off sooner than this because of the back emf caused by motion, and because the above doesn't allow for the winding resistance. Low inductance motors also have low back emf due to rotation. - -> What this means is that if we want to achieve high speeds, we need low inductance motors and high supply voltage. So, we must choose the 1.8 A stepper motor having lower inductance (3.2 mH) compared to the 0.4 A stepper motor (58 mH). - -## General Recommendations ---- -- Choose motors with rated current of at least 1.2 A. - -- Plan to run each stepper motor at between 50% and 85% of its rated current. - -- Nema 17 is the most popular size used in 3D printers. Nema 14 is an alternative in a highly-geared extruder. Use Nema 23 motors if you cannot get sufficient torque from long Nema 17 motors. - -- Avoid motors with rated voltage (or product of rated current and phase resistance) > 4 V or inductance > 4 mH. - -- Choose 0.9 deg/step motors where you want extra positioning accuracy, e.g. for the tower motors of a delta printer. Otherwise choose 1.8 deg/step motors. - -- If you use any 0.9 deg/step motors, or high torque motors, use 24V power so that you will be able to maintain torque at higher speeds. - - - - diff --git a/docs/mechanics/3D Printer Mechanics.md b/docs/machines/3DPrinter/3D Printer Mechanics.md similarity index 100% rename from docs/mechanics/3D Printer Mechanics.md rename to docs/machines/3DPrinter/3D Printer Mechanics.md diff --git a/docs/machines/3DPrinter/Step by Step Assembly.md b/docs/machines/3DPrinter/Step by Step Assembly.md index 75482bbd7e1dc76a1dfbf7761df733b05c504dd2..f61b448ba67747a206fd1fc372866b97c46f9eff 100644 --- a/docs/machines/3DPrinter/Step by Step Assembly.md +++ b/docs/machines/3DPrinter/Step by Step Assembly.md @@ -1,11 +1,11 @@ # Build Instructions -The build instructions below are divided into two parts, namely pre-assembly and final assembly. In the pre-assembly some of the sub-assmeblies or parts are either prepared or assembled together to ease the final assembly. The numbering system below will be referred to within the build manual by appending each number after the previous number for eg. the LM12UU bearing installation is in step **1.4.1** and can be looked up in the list below as part of the Build Platform assembly > Z-Axis Bearing Holder > LM12UU Bearing. The number in the (#) paranthesis denotes the quantity of the part. +The build instructions below are divided into two parts, namely pre-assembly and final assembly. In the pre-assembly some of the sub-assmeblies or parts are either prepared or assembled together to ease the final assembly. The number in the (#) paranthesis denotes the quantity of the part required. ## Pre-Assembly ### 1. Y-axis Left Pre-assembly (1) - + Parts required: 1. XY Idler Assembly Left (1) diff --git a/docs/machines/DesktopLaserCutter.md b/docs/machines/DesktopLaserCutter.md index ce3d6e4c46a0f5821d581e9312a1924f6345205f..51149936fe513a49190d6cb547b677f9b5fae4bf 100644 --- a/docs/machines/DesktopLaserCutter.md +++ b/docs/machines/DesktopLaserCutter.md @@ -1,7 +1,13 @@ # Desktop Laser Cutter -[DIY Laser Cutter Fume Extractor](https://www.instructables.com/Build-a-laser-cutter-fume-extractor/) +1. [LaserDUO](http://laserduo.com/) +  + +2. [Fabulaser](http://fabulaser.net/) + 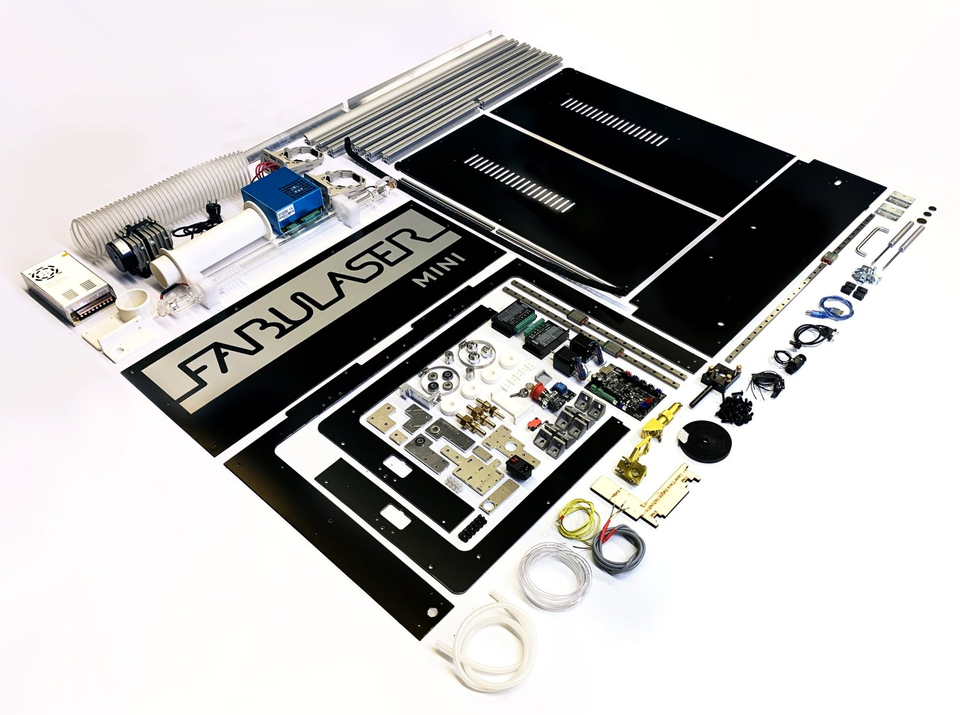 + +3. [Lasersaur](https://www.lasersaur.com/) + -1. LaserDUO - Daniele Ingrassia -2. Lasermini - Daniele Ingrassia -3. \ No newline at end of file + +[DIY Laser Cutter Fume Extractor](https://www.instructables.com/Build-a-laser-cutter-fume-extractor/) diff --git a/docs/machines/DesktopMillingMachine.md b/docs/machines/DesktopMillingMachine.md index 1b18daa67fe42e63f0fbcf8258701c15dc8e638a..94292512a2188bbfd95818c48db09ce80609e3ef 100644 --- a/docs/machines/DesktopMillingMachine.md +++ b/docs/machines/DesktopMillingMachine.md @@ -51,6 +51,10 @@ - Design files and details - [https://www.thingiverse.com/thing:4644222] - CAD files on Grabcad - [https://grabcad.com/library/rock-solid-cnc-router-with-1-5kw-spindle-1] +16. [VriMech Desktop Milling](https://vrimech.com/desktop-cnc-mill/) Machine made from Aluminium profiles and aluminium plates + - Engineering drawings and CAD model available (original source CAD) + -  + - Made from profiles and drilled holes on plates can be made using simple tools ## Commercial Desktop CNC Mills diff --git a/docs/mechanics/Ball Screws.md b/docs/mechanics/Ball Screws.md index e3c669f8954b08e4a098e9daf61c31c409094d32..122521f6d9e5e00478a2f79ddd1f9792fb797fa9 100644 --- a/docs/mechanics/Ball Screws.md +++ b/docs/mechanics/Ball Screws.md @@ -37,5 +37,5 @@ There are several disadvantages. For your particular application, you need to evaluate the tradeoffs. Either could be your answer. If the analysis is too complex, you could default to belt drive. You could put the money you would have spent on ball screws, ball nuts, and extra bearings into wider belts, higher torque motors with smaller step angles, and better (higher voltage, faster switching) motor drives. - There are two types of ball screws- rolled and ground. The cheap chinese ones are the rolled ones and specs won't be as good as the ground screws. -- + [Information](https://www.machinedesign.com/mechanical-motion-systems/linear-motion/article/21828146/the-importance-of-ballscrew-end-fixity) on fixing methods of ball screw ends and their importance \ No newline at end of file diff --git a/docs/mechanics/Belts and Pulleys.md b/docs/mechanics/Belts and Pulleys.md index 13385f2a5724acd1b73694427f1ff243450e37a2..f6bce6834b020e9ec252f8da14abe91cf26e79aa 100644 --- a/docs/mechanics/Belts and Pulleys.md +++ b/docs/mechanics/Belts and Pulleys.md @@ -1,6 +1,7 @@ # Motion Systems There are various mechanisms used for transmitting the motion on the X,Y and Z axes. Some of the most commonly used types are: + 1. Rollers (Delrin wheels, metal rollers, bearings etc) rolling either on or within a straight or profiled extrusion (V-Rails) - Delrin wheels rolling within the V-slot grooves of a Aluminium V-slot extrusion profile. These are most commonly used in budget DIY 3D printers, since they are ideally suited for low load applications. - Pros: